Dessiner en 3D pour la MakerBot – Conseils et astuces de design
Publié le 16 janvier 2014Chapitre 8 du livre « Imprimer en 3D avec la MakerBot » posté sous la forme d’articles :
Ce chapitre propose quelques tutoriels détaillés faisant appel aux modeleurs 3DTin, Tinkercad, 123D et SketchUp, qui vous permettront de transformer vos modèles 3D d’objets en impressions 3D bien réelles.
Maintenant que vous avez pu apprécier la satisfaction immédiate que procure l’impression 3D, il est temps d’explorer les capacités de prototypage rapide de votre MakerBot, en concevant vos propres objets. Vous avez probablement déjà de nombreuses idées et c’est même sûrement pour cela que vous avez acheté cette imprimante !
Une fois que vous aurez assimilé les contraintes de design propres à l’impression 3D, vous serez en mesure de vous lancer dans la création d’objets. Dans ce chapitre, nous allons vous présenter quelques logiciels de modélisation 3D, accompagnés de tutoriels, qui transformeront votre bureau en une usine tournant à plein régime.
Conseils et astuces de design
Voici quelques recommandations générales sur la conception de vos objets destinés à être imprimés par une MakerBot. Tant que vous les garderez bien en tête, votre champ de création sera libre de toute contrainte.
Limitations techniques de l’imprimante
Quand vous dessinez un objet en vue d’une impression 3D, vous devez tenir compte des limitations techniques de votre MakerBot. Il faut savoir que le niveau de résolution du système de positionnement est inférieur au millimètre. Pour la Thing-O-Matic, les axes X et Y peuvent être contrôlés à 85 microns près et l’axe Z à 4 microns. Pour la série Replicator, dont l’électronique et le support mobile ont été améliorés, cette résolution est de 11 microns pour les axes X et Y, et de 2,5 microns pour l’axe Z.
Notez bien que cela ne signifie pas que votre MakerBot sera capable d’imprimer des objets de 0,01 mm. L’épaisseur minimale d’impression dépend aussi d’autres facteurs, comme la taille de la buse ou le matériau d’impression. En effet, même si la MakerBot peut positionner la goutte de plastique qui sort de l’extrudeur avec une incroyable précision, le filament possédera toujours une certaine épaisseur. La véritable qualité d’une impression dépend donc de la résolution par couche, qui est fonction de la précision de l’axe Z, de la taille de la buse et des performances de l’extrudeur. Sur la Replicator 2, la résolution minimale par couche est de 100 microns, valeur 2,5 fois inférieure à celle de la première Replicator. Cela signifie que vous serez capable d’imprimer avec une telle finesse que vous ne pourrez même pas distinguer les différentes couches à l’oeil nu ! Ainsi, vous passerez moins de temps à poncer et polir vos objets, et vous en aurez plus pour dessiner et imprimer.
Porte-à-faux et ponts
Un porte-à-faux est une partie d’un objet située au-dessus du vide. Étant donné qu’une MakerBot travaille couche par couche, il peut donc être difficile de fabriquer un objet comportant ce type d’élément, sans points d’appui suffisants. Mais comme la goutte de plastique n’est pas de largeur nulle, il reste possible de fabriquer un porte-à-faux si on introduit un très léger décalage en déposant chaque couche de matériau sur la précédente. À titre de comparaison, imaginez une pièce de monnaie en équilibre sur le bord d’une table, ou une pile de livres un peu décalée par rapport à la verticale. La règle des 45 degrés stipule qu’un porte-à-faux ne dépassant pas 45° d’inclinaison au-dessus du vide doit pouvoir être imprimé sans problème. Mais si votre objet en comporte beaucoup, il risque parfois d’être un peu filandreux ou pelucheux au niveau de ces zones (voir figure 8-1). Cela dit, beaucoup de designers sur Thingiverse utilisent des porte-à-faux pour créer des objets incroyables.
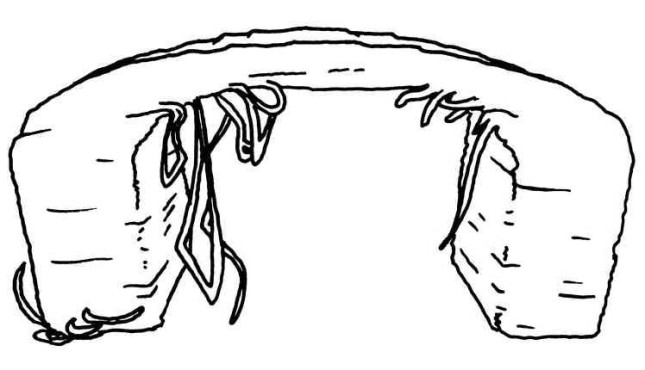
Figure 8-1. Les porte-à-faux peuvent entraîner des affaissements de matière et des couches filamenteuses
Si vous rencontrez ce genre de problème, une solution consiste à découper le plastique en excédent, puis à poncer les zones affectées. Attention toutefois, car le ponçage risque d’endommager l’objet. Aussi, consultez la section « Finition de surface » (voir page 109) avant de vous lancer dans cette opération.
Outre les porte-à-faux, la Replicator 2 permet également de fabriquer des ponts. Grâce à sa grande vitesse d’impression et à l’élasticité du matériau, il est en effet possible de créer de courtes passerelles de plastique entre deux points sans le moindre support. Si votre objet comporte deux zones séparées par un vide, l’extrudeur peut étirer entre elles une goutte de plastique, et une fois celle-ci solidifiée, imprimer par-dessus. Mais il s’agit d’une technique avancée dont le succès n’est pas garanti. Il dépendra du matériau utilisé, de la vitesse de déplacement, de la température et… de la phase de la lune. Si l’objet possède beaucoup de ponts, le plastique aura tendance à s’affaisser. Ce défaut pourra cependant être facilement corrigé en découpant le plastique excédentaire avec un outil coupant. MakerWare calculera automatiquement les déplacements nécessaires de l’extrudeur pour réaliser des ponts.
Toutefois, la contrainte des 45 degrés et les défauts liés aux ponts peuvent être facilement supprimés de différentes manières. Ainsi, vous pouvez utiliser l’option de MakerWare qui permet de générer automatiquement des structures de support. Ces petits morceaux de plastique sont ajoutés à l’objet pour supporter les zones en porte-à-faux ; une fois l’impression terminée, elles sont très faciles à retirer. La figure 8-2 présente un support qui a été retiré d’une arche.
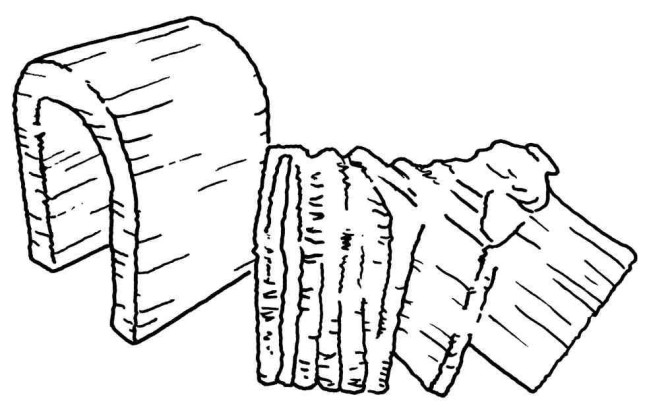
Figure 8-2. Un support retiré d’un objet imprimé
Une autre solution pour s’affranchir de ces contraintes de fabrication consiste à créer manuellement une structure, qui soutiendra les zones non traitées par MakerWare. Par exemple, l’ajout de murs de 0,35 mm tous les 1 cm devrait être plus que suffisant pour créer un pont au-dessus d’un vide. Si aucune de ces solutions n’est envisageable, le designer aura toujours la possibilité de scinder virtuellement l’objet en plusieurs pièces qui pourront être imprimées sans porte-à-faux, puis tout réassembler après impression.
Mais dans certains cas, il vous suffira de faire pivoter l’objet sur la plateforme virtuelle de MakerWare. Ainsi, la voûte de la figure 8-2 n’aurait nécessité aucun support si elle avait été tout simplement retournée.
Étanchéité
Pour un nouvel utilisateur de MakerBot, la création ou l’obtention d’un objet étanche est certainement l’une des tâches les plus ennuyeuses. Votre fichier STL doit en effet représenter un objet continu et solide : s’il comporte des trous, des vides, des sommets et/ou des faces qui se chevauchent dans le modèle, le logiciel d’impression 3D ne sera pas capable de distinguer l’intérieur de l’objet de l’extérieur. Heureusement, des outils existent pour localiser ces trous et les fermer, mais pour de meilleurs résultats, il est préférable de les éviter dès le début, au moment où vous dessinez l’objet. Toutefois, si votre logiciel de modélisation ne parvient pas à vous fournir un objet étanche, vous pourrez toujours réparer le fichier STL avec des outils comme MeshMixer ou netfabb. Pour en savoir plus, consultez le chapitre 9.
Déformation des coins
Si vous avez dessiné un objet très long, large et plat, les coins risquent de se courber pendant l’impression. En effet, quand le plastique extrudé refroidit, il se contracte légèrement. Ce problème affecte plus fortement l’ABS, mais le PLA est également concerné. La solution la plus simple pour éviter ce problème est de prévoir un raft, autrement dit un large treillis imprimé sous la première couche de la pièce, pour permettre à cette dernière d’adhérer à la plate-forme.
Pour pallier ce défaut, certains utilisateurs impriment des cloisons ou des enceintes de protection qui entourent le plateau d’impression. Le but de ces parois est d’empêcher l’arrivée d’air froid sur la base du modèle et de maintenir l’objet à une température relativement constante. Les designers qui travaillent chez MakerBot tiennent souvent compte de ce problème dès la conception de leurs objets, en y ajoutant dans les coins des mouse ears (littéralement, oreilles de souris). Il s’agit de petites structures circulaires et planes qui jouent le rôle de mini-rafts, en permettant à l’objet de mieux adhérer à la plate-forme et de refroidir de façon plus uniforme.
Même si vous imprimez avec du PLA , vous partagerez probablement votre modèle (voir chapitre10) avec des makers qui utiliseront de l’ABS ou une imprimante 3D moins récente et plus contraignante. Il vaut donc mieux connaître ces contraintes, même si vous imprimez en PLA sur une Replicator2 sans rencontrer le moindre problème.
Engrenages et pièces mobiles
Lorsque vous créez un modèle 3D qui comporte des pièces mobiles, telles que des engrenages , des rouages ou des maillons de chaîne, pensez à prévoir suffisamment d’espace entre elles. S’il n’y en a pas assez, vous risquez en effet de vous retrouver avec un objet monobloc. Un interstice de 0,4 ou 0,5 mm sur chaque côté suffi t normalement pour un élément mobile. Pour ceux qui doivent s’emboîter parfaitement, un espace de 0,1 à 0,25 mm est préférable pour éviter qu’ils se désolidarisent.
Sur le site de Thingiverse, vous trouverez deux exemples intéressants d’objets avec parties mobiles : le MakerBelt de makerbot et le Chain Generator de Sal.
Un bon exemple d’impression flexible est la prodigieuse cotte de mailles de Zomboe, dont PrettySmallThings s’est inspirée pour créer un maillage pour sac à main . Le Printable Brain Gear est un excellent exemple de rouages devant s’ajuster parfaitement.
Design d’une pièce de dimensions précises
La Replicator 2 est une machine d’une précision redoutable. Néanmoins, les ingénieurs et les designers qui souhaiteront des pièces de dimensions très précises devront se souvenir que l’ABS se contracte de 2 % après refroidissement. Quant au PLA, il rétrécit de 0,2 %, ce qui en fait un matériau plus approprié pour un travail de précision. Dans tous les cas, pensez à tenir compte de cette contraction lorsque vous concevez un objet destiné à être imprimé sur une MakerBot.
Finition de surface
Pour obtenir une surface bien lisse, voici quelques principes à retenir. Il faut déjà savoir que les surfaces courbes possèdent généralement un aspect plus doux que les planes, car pour les imprimer, l’extrudeur suit un chemin fermé, sans discontinuités. Par conséquent, si vous dessinez un mur très fin, d’une épaisseur égale à celle de l’extrudeur, il devra constituer une courbe fermée ou être relativement long, sinon le résultat ne sera pas satisfaisant. En revanche, si vous lui donnez deux ou quatre épaisseurs, il deviendra sa propre courbe fermée. Toutefois, les objets correspondant à de courts trajets de l’extrudeur demeurent généralement problématiques, même si ces chemins sont des courbes fermées, car le matériau n’a pas suffisamment de temps pour refroidir (malgré l’aide active du ventilateur de la Replicator 2).
Quel que soit le modèle 3D, une petite finition est toujours la bienvenue. Les objets peuvent ainsi être poncés et peaufinés. Dans le cas de pièces en ABS, un peu d’acétone permettra d’atténuer les petits défauts. Certains utilisent un vernis, de la peinture à base d’émail, de la résine époxy ou de la peinture en aérosol pour lisser la surface.
Des finitions d’aspect métallique ont été également mises au point. Ainsi, Cosmo Wenman se prépare à distribuer sa ligne de patines très réalistes, comme on peut le voir sur sa tête d’Alexandre le Grand et ses autres sculptures incroyables. De son côté, le site Metal2Create propose pour les projets imprimés en 3D une finition à base de vrai métal, sous forme de poudre.
On peut obtenir une surface très douce en appliquant plusieurs couches fines de peinture en spray Krylon Fusion. Cette peinture s’accroche facilement au plastique, sans ponçage préalable, ce qui permet de conserver un maximum de petits détails. Je ponce ensuite les petits défauts avec du papier de verre d’un grain de 100 et repeins si nécessaire, jusqu’à ce que les lignes d’impression ne soient plus visibles. Anna Kasiunas France
N’hésitez pas à tenter des expériences, car il existe de nombreuses techniques et aucune d’elles ne peut se prévaloir d’être universelle.
Faites abstraction du volume d’impression
En dessinant vos objets, vous vous demanderez tôt ou tard quel est le plus grand modèle que votre MakerBot puisse imprimer. Comme on l’a vu dans le chapitre 5, le volume d’impression de la Replicator 2 est de 28,5 × 15,3 × 15,5 cm, ce qui correspond à la taille maximale d’un seul objet. Mais si vous vous organisez intelligemment, vous ne serez pas limité par les dimensions de la machine. Si vous faites abstraction du plateau d’impression et transformez votre projet en pièces à assembler ultérieurement, vous pouvez fabriquer des objets beaucoup plus grands.
Pour assembler ces différentes pièces, vous pourrez utiliser des connecteurs, comme le Pin Connectors v2 développé avec openSCAD par TonyBuser. Consultez aussi la page des objets dérivés pour apprécier l’étendue des possibilités offertes par ce petit objet.
Dans la pure tradition de Thingiverse, ce connecteur a ensuite été repris et amélioré par emmett, qui a mis au point le Pin Connectors 3 et l’a utilisé sur son modèle de transmission automatique et sur son moteur à chemises louvoyantes ou chemises-tiroirs (sleeve valve engine).
La tête du cheval de Séléné, réalisée par Cosmo Wenman, est un autre exemple remarquable d’objet en pièces détachées. Cette sculpture donne également un aperçu de l’excellente qualité que l’on peut obtenir en matière de finition. Ce modèle a été découpé en plusieurs parties dans nettfabb, puis les pièces ont été imprimées séparément avant d’être collées. Pour finir, la surface a été recouverte avec l’une des patines réalistes évoquées plus haut. Le chapitre 9 vous en apprendra davantage sur le tranchage des modèles 3D avec nettfabb.
Solidité
Bien que le matériau d’impression soit assez résistant en lui-même, un objet imprimé en 3D ne sera pas aussi robuste qu’une pièce moulée ou usinée, puisqu’il est composé d’une série de couches. Plus précisément, sa résistance ne sera pas la même dans toutes les directions : il sera plus fragile entre les couches que sur les axes X ou Y. Soumises à des contraintes extrêmes, les couches sont d’ailleurs connues pour se délaminer. Il faut s’en souvenir si l’on souhaite concevoir des pièces résistantes.
Tout au long de ce chapitre, nous avons évoqué les forces et les faiblesses de l’ABS et du PLA. C’est un débat qui anime la communauté de l’impression 3D et trouve peu de réponses satisfaisantes. Par exemple, si le PLA se contracte moins que l’ABS, cela ne signifie pas pour autant que ce soit un matériau supérieur. En effet, pour beaucoup d’objets, cette propriété de l’ABS permet de fabriquer des ponts et des porte-à-faux plus réussis.
Une chose est certaine : l’ABS est plus ductile, ce qui signifie qu’il se déformera et s’écoulera plus facilement. Certains éléments comme les charnières actives et les fixations à pression, qui reposent sur de bonnes propriétés de déformation, sont des exemples parfaits où l’ABS sera plus adapté. En outre, ce matériau réagira mieux aux contraintes physiques : les pièces en ABS auront tendance à plier et à s’étirer quand celles en PLA craqueront ou rompront. Par ailleurs, l’ABS supporte mieux d’être percé et taraudé. Mais tous ces aspects ne sont que pures généralités, car d’un fabriquant à un autre (et parfois même d’un coloris à l’autre), les propriétés d’un ABS varient. Pour mieux comprendre les limites de ces matériaux, il ne vous reste qu’une chose à faire : expérimentez et imprimez sans compter, c’est l’un des plaisirs liés à la possession d’une MakerBot !
Mise à l’échelle et redimensionnement
Si vous souhaitez fabriquer un objet avec des dimensions très précises, vous devrez le dessiner à l’échelle dans le logiciel de modélisation, en tenant compte de la contraction du plastique. Notez que la plupart de ces modeleurs offrent également la possibilité de redimensionner une pièce. Sinon, vous pourrez facilement mettre votre modèle à l’échelle dans MakerWare.
Si vous avez un Mac, vous pourrez utiliser Pleasant3D, un logiciel bien pratique pour redimensionner des fichiers STL. Cet outil est aussi un visualiseur de G-code et un convertisseur ASCII-binaire pour le format STL.TL.